Understanding the Basics and Applications of Plastic Extrusion in Modern Production
In the realm of modern-day production, the method of plastic extrusion plays an instrumental duty - plastic extrusion. This intricate process, involving the melting and shaping of plastic through specialized dies, is leveraged across numerous sectors for the creation of diverse items. From auto components to durable goods packaging, the applications are substantial, and the capacity for sustainability is equally outstanding. Untangling the principles of this process exposes truth adaptability and possibility of plastic extrusion.
The Basics of Plastic Extrusion Process
While it might show up facility, the fundamentals of the plastic extrusion procedure are based upon reasonably straightforward principles. It is a production procedure wherein plastic is melted and then formed right into a continual account through a die. The raw plastic material, often in the type of pellets, is fed into an extruder. Inside the extruder, the plastic undergoes warmth and pressure, causing it to melt. The molten plastic is then required with a shaped opening, understood as a die, to form a long, continuous product. The extruded product is cooled and after that cut to the preferred size. The plastic extrusion process is thoroughly utilized in various industries because of its cost-effectiveness, efficiency, and versatility.
Different Sorts Of Plastic Extrusion Strategies
Structure upon the fundamental understanding of the plastic extrusion process, it is required to check out the numerous strategies included in this production technique. The 2 primary methods are profile extrusion and sheet extrusion. In profile extrusion, plastic is melted and developed right into a constant profile, commonly made use of to develop pipelines, rods, rails, and window structures. In contrast, sheet extrusion develops huge, level sheets of plastic, which are commonly further processed right into items such as food product packaging, shower curtains, and cars and truck components. Each method requires specialized equipment and specific control over temperature level and pressure to guarantee the plastic preserves its form throughout cooling. Recognizing these techniques is essential to using plastic extrusion effectively in modern manufacturing.
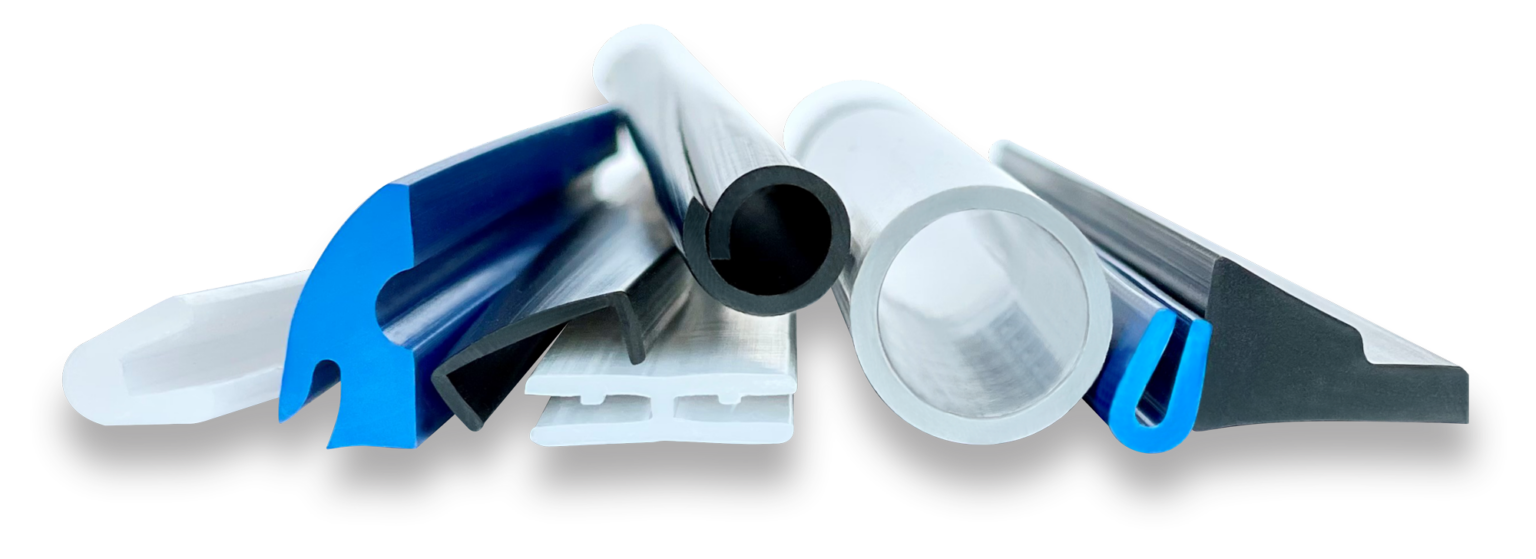
The Role of Plastic Extrusion in the Automotive Sector
A frustrating majority of parts in modern cars are items of the plastic extrusion process. This process has transformed the vehicle industry, changing it into a much more reliable, economical, and flexible manufacturing market. Plastic extrusion is mostly utilized in the manufacturing of various automobile parts such as bumpers, grills, door panels, and dashboard trim. The procedure gives an uniform, constant result, making it possible for producers to generate high-volume get rid of excellent precision and marginal waste. The agility of the extruded plastic parts contributes to the overall decrease in automobile weight, improving gas effectiveness. The toughness and resistance of these parts to warm, cold, and influence boost the durability of cars. Hence, plastic extrusion plays a crucial duty in automotive manufacturing.
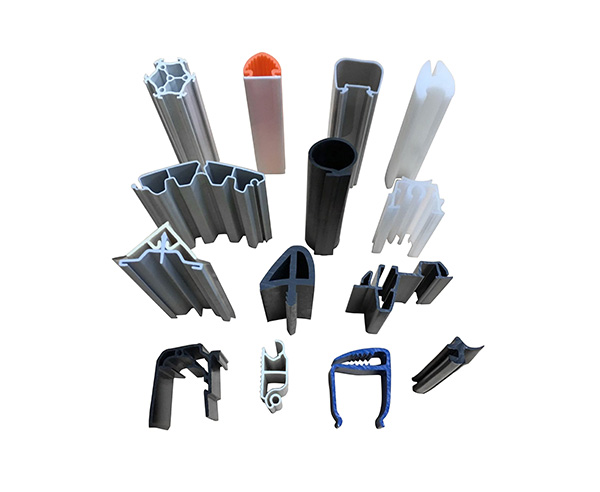
Applications of Plastic Extrusion in Customer Goods Manufacturing
Past its substantial impact on the automobile market, plastic extrusion confirms just as effective in the world of durable goods making. This procedure is essential in developing a vast array of items, from food packaging to family home appliances, toys, and even medical devices. The versatility of plastic extrusion enables suppliers to create and produce intricate sizes and shapes with high precision and effectiveness. Due to the recyclability of many plastics, squeezed out components can be reprocessed, lowering waste and price (plastic extrusion). The versatility, adaptability, and cost-effectiveness of plastic extrusion make it a recommended selection for several customer products manufacturers, adding significantly to the sector's development and advancement. Nonetheless, the check my site ecological effects of this prevalent use require mindful factor to consider, a subject to be talked about further in the succeeding area.
Ecological Effect and Sustainability in Plastic Extrusion
The prevalent use of plastic extrusion in producing welcomes scrutiny of its eco-friendly implications. As a process that frequently utilizes non-biodegradable materials, the environmental impact can be considerable. Energy consumption, waste production, and carbon discharges are all problems. Industry developments are raising sustainability. Effective machinery lowers energy usage, while waste administration systems recycle scrap plastic, decreasing read here basic material demands. Furthermore, the advancement of biodegradable plastics supplies a more eco-friendly choice. Despite these improvements, even more advancement is needed to mitigate the environmental impact of plastic extrusion. As society leans towards sustainability, makers need to adjust to stay sensible, highlighting the significance of continual research study and development in this field.
Verdict
To conclude, plastic extrusion plays an essential function in modern production, especially in the vehicle and durable goods fields. Its versatility enables the production of a variety of parts with high precision. Its capacity for reusing and growth of naturally degradable products uses a promising opportunity in the direction of sustainable techniques, consequently attending to environmental problems. Comprehending the fundamentals Full Report of this procedure is key to maximizing its applications and benefits.
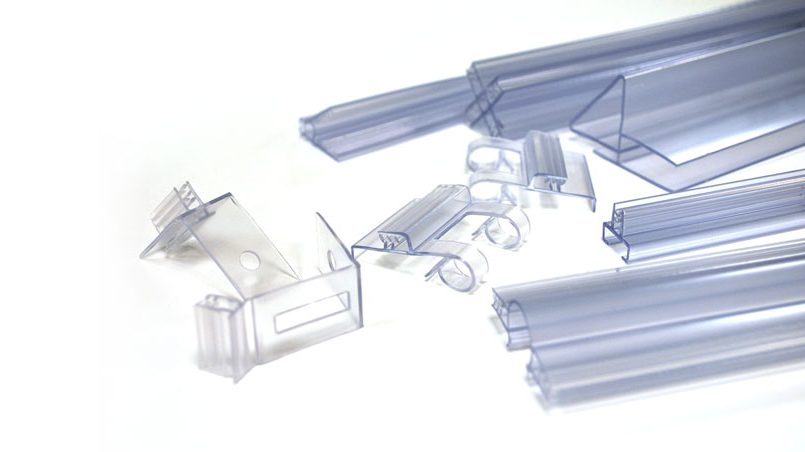
The plastic extrusion procedure is thoroughly utilized in numerous markets due to its adaptability, cost-effectiveness, and performance.
Building upon the fundamental understanding of the plastic extrusion procedure, it is necessary to explore the various strategies entailed in this production technique. plastic extrusion. In contrast, sheet extrusion produces huge, level sheets of plastic, which are normally more refined right into products such as food packaging, shower curtains, and cars and truck components.An overwhelming majority of parts in modern automobiles are items of the plastic extrusion process
Comments on “Plastic extrusion for thermoplastics, PVC, and engineering plastics”